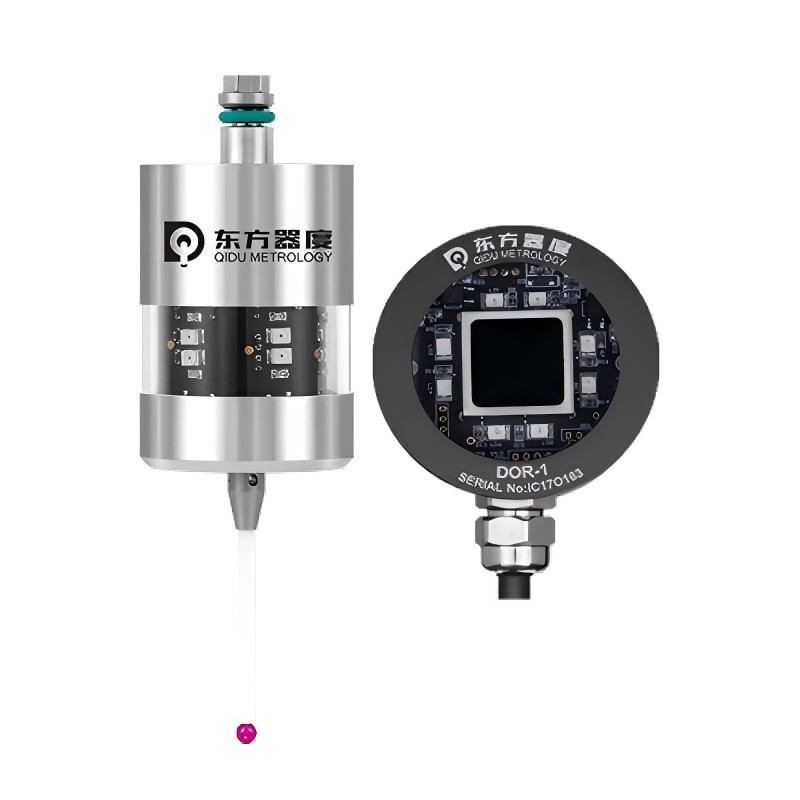
CNC Touch Probe Introduction
In the field of CNC machining, CNC Touch Probe (CNC touch probe) is an important device to improve machining accuracy and efficiency. It can accurately obtain relevant data of workpieces and tools, providing key support for the machining process.
Working Principle
The CNC touch probe triggers the signal by contacting the probe with the surface of the object being measured. When the probe contacts the surface of the workpiece or tool, the trigger mechanism inside the probe will produce a small displacement, which will cause the electrical signal to change. This signal change is transmitted to the CNC system. The system calculates the exact position of the probe contact point in the coordinate system based on the pre-set algorithm and the machine tool coordinate system, thereby obtaining information such as the size and shape of the workpiece and the position and wear of the tool.
Features of CNC Touch Probe
- High-precision measurement: The probe has extremely high triggering accuracy, usually up to micron level, and can accurately measure the complex contours and small size changes of the workpiece to meet the needs of high-precision machining.
- Compact structure: The design is compact and small, easy to install on the machine tool workbench or in the tool magazine, does not take up too much space, and can also flexibly measure workpieces and tools in different positions.
- Multiple probe options: Equipped with a variety of probes of different shapes and lengths, such as ruby ball probes, star probes, etc., which can be adapted according to different measurement tasks and surface characteristics of the measured object to ensure the accuracy and reliability of measurement.
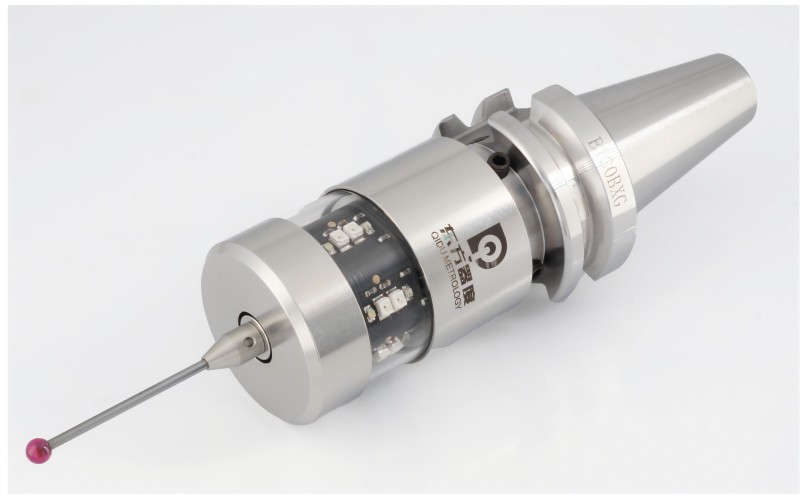
Application scenarios of CNC Touch Probe
- Workpiece measurement: Before part processing, measure the blank to check whether its size meets the requirements so as to adjust the processing technology in time; during processing, monitor the workpiece size in real time, compensate for the processing error, and ensure the processing accuracy; after processing, conduct a comprehensive inspection of the finished product to ensure that the product quality meets the standards.
- Tool measurement: Measure the length, diameter, tool wear and other parameters of the tool, and timely detect the wear and damage of the tool so as to replace the tool or adjust the tool compensation value to ensure the processing quality and efficiency.
- Mold manufacturing: During the mold processing process, the complex shapes of the mold cavity, core, etc. are accurately measured to ensure the manufacturing accuracy of the mold and improve the service life and product quality of the mold.
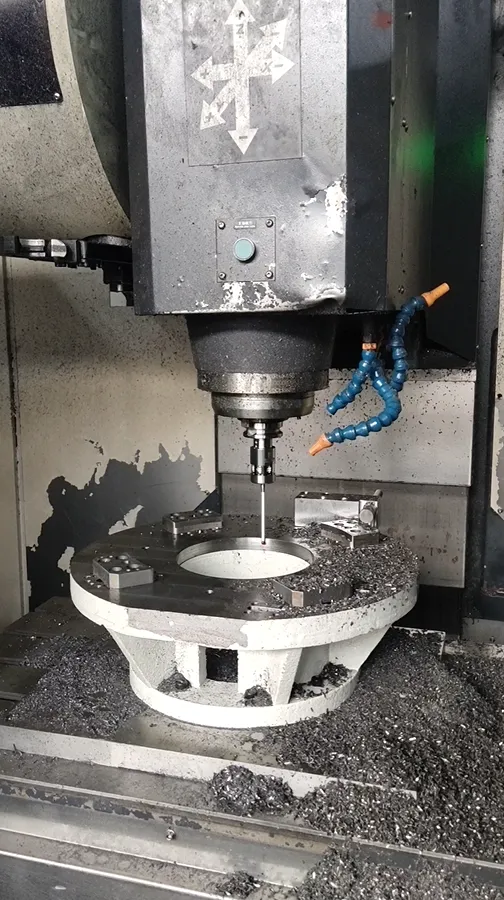

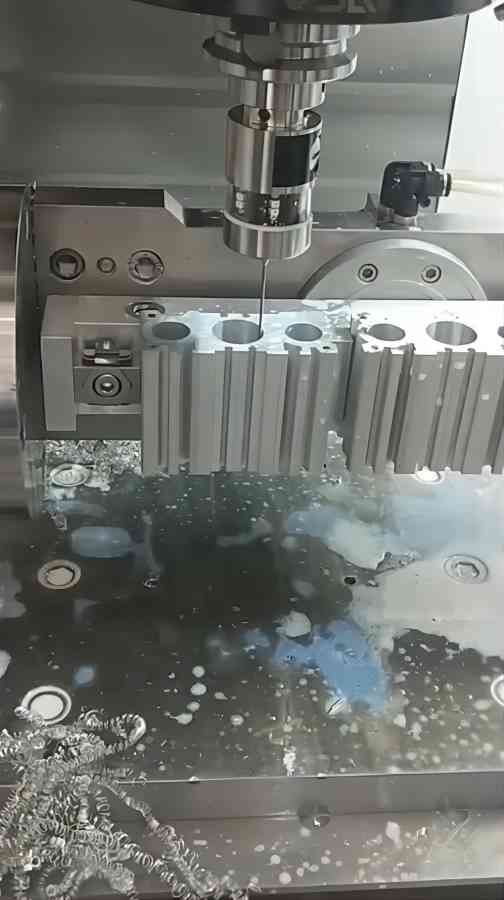
Advantages
- Improve processing quality: Through real-time measurement and error compensation, effectively reduce processing errors, improve the processing accuracy and surface quality of the workpiece, and reduce the scrap rate.
- Shorten the processing cycle: reduce the time of manual measurement and adjustment, realize the seamless connection of automated measurement and processing, improve the utilization rate of machine tools, and shorten the production cycle of products.
- Reduce production costs: reduce waste and rework caused by processing errors, reduce production costs; at the same time, due to the improvement of processing efficiency, it also indirectly reduces the production cost of each unit product.
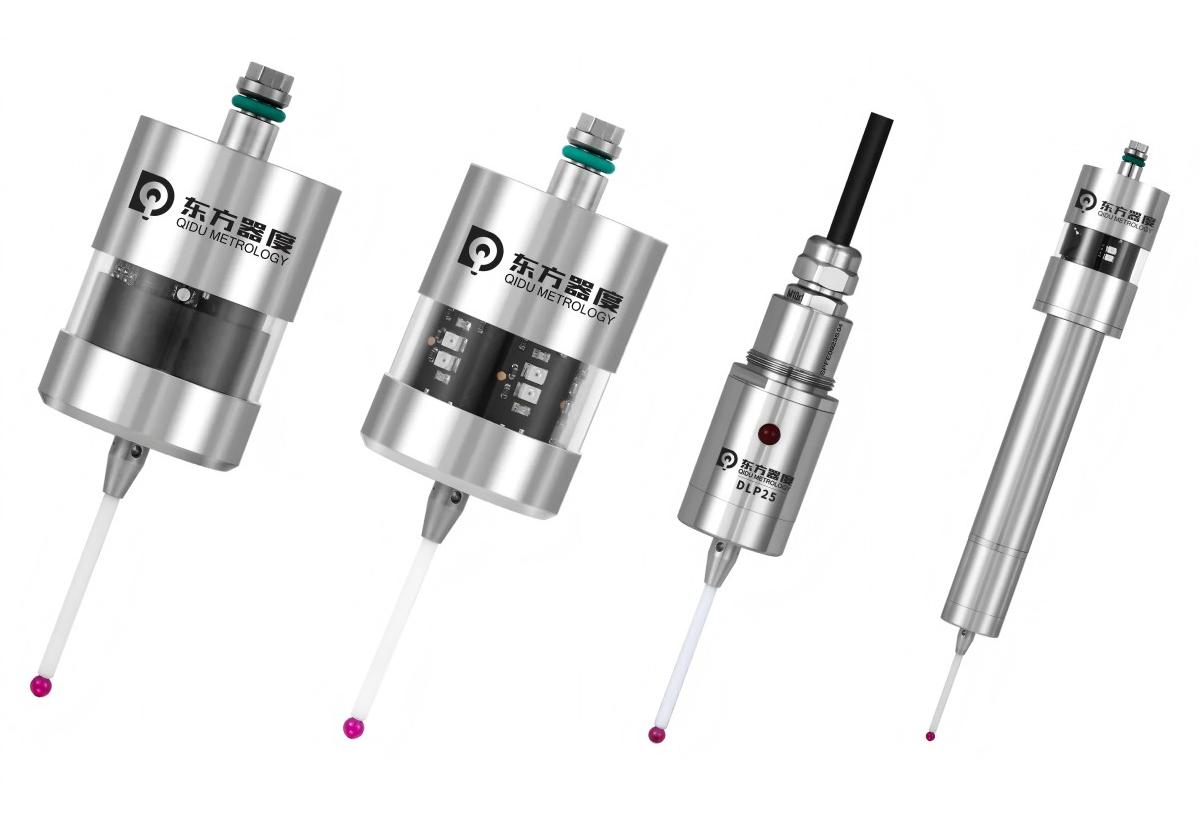